เชื่อมโยงผู้คนผ่านวิศวกรรมเพื่อการปรับปรุงผลิตภาพและคุณภาพที่ดียิ่งขึ้น
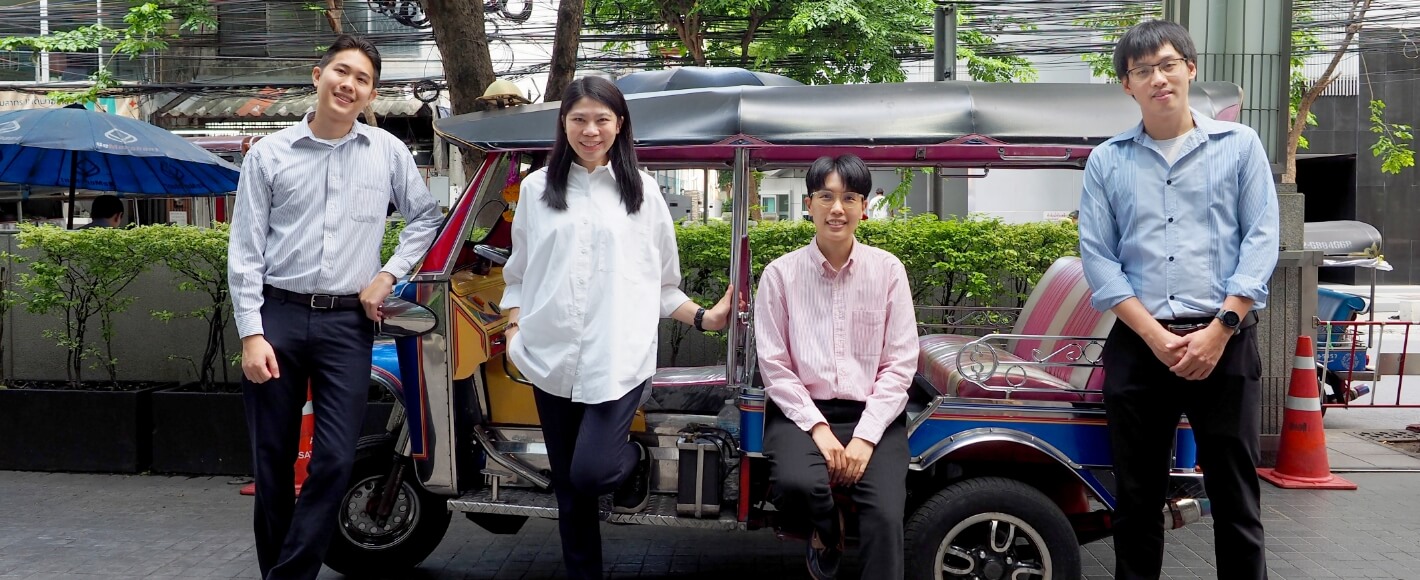
บริษัท Mitsubishi Electric มีฐานการผลิตและกลุ่มบริษัทกระจายอยู่ทั่วโลก หนึ่งในนั้นคือบริษัท Mitsubishi Electric Asia (Thailand) หรือ ME-TH เป็นสำนักงานประจำภูมิภาคเอเชีย ตั้งอยู่ที่กรุงเทพฯ นอกจากนี้ในประเทศไทยยังมีโรงงานที่เป็นฐานการผลิตของกลุ่ม Mitsubishi Electric อยู่ถึงหกบริษัทด้วยกัน ซึ่งทำหน้าที่เป็นฐานการผลิตของผลิตภัณฑ์อันหลากหลายป้อนสู่ตลาดโลกจึงทำให้ประเทศไทยถือเป็นฐานการผลิตที่สำคัญของกลุ่มบริษัท Mitsubishi Electric
ภายในองค์กรของ ME-TH เรามีแผนกวิศวกรรมการผลิต (Manufacturing Engineering) ซึ่งมีหน้าที่เผยแพร่และสนับสนุนในด้านความรู้เฉพาะทางและเทคโนโลยีให้กับโรงงานต่างๆในกลุ่ม Mitsubishi Electric เพื่อช่วยปรับปรุงผลิตภาพ (Productivity) และคุณภาพของผลิตภัณฑ์ให้ดียิ่งขึ้น ในบทความนี้จะแนะนำถึงกิจกรรมและลำดับความสำคัญของแผนกวิศวกรรมการผลิตผ่านการสัมภาษณ์สมาชิกในแผนกทั้งสี่ท่าน
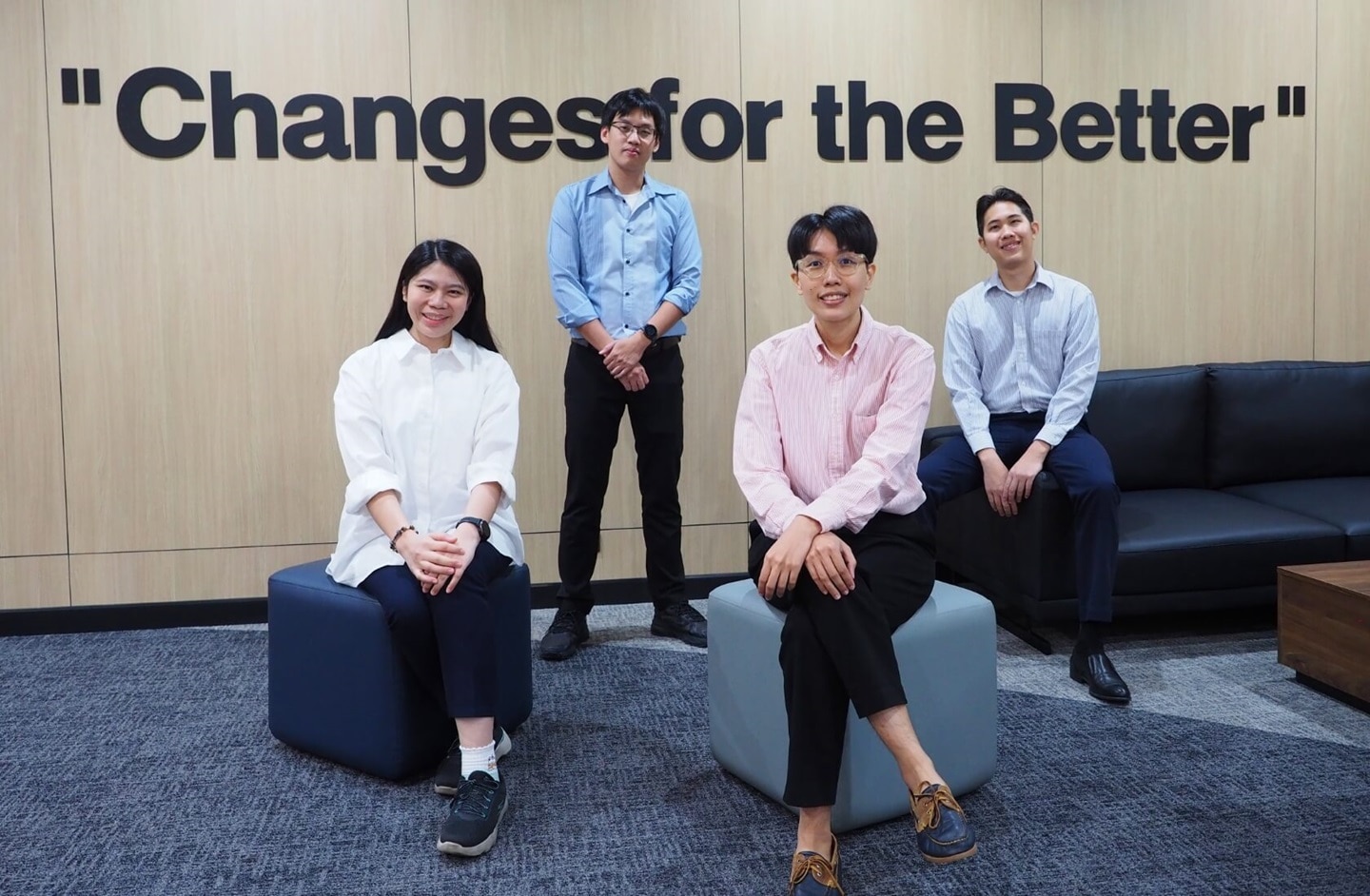
จากซ้ายไปขวา:
คุณมัสลิน สิริขวัญวิวัฒน์ (ฝ้าย) ผู้ช่วยผู้จัดการ แผนกวิศวกรรมการผลิต
คุณกิตติพงษ์ ต่อสกุลรัตน์ (ป๊อบ) ผู้ช่วยผู้จัดการ แผนกวิศวกรรมการผลิต
คุณสันสณี เที่ยงคำดี (น้ำ) ผู้ช่วยผู้จัดการ แผนกวิศวกรรมการผลิต
คุณอานันท์ ฤทธิ์ฤาดี (อานันท์) วิศวกรอาวุโส แผนกวิศวกรรมการผลิต
แผนกวิศวกรรมการผลิต: ผู้เชี่ยวชาญด้านการปรับปรุงการผลิต
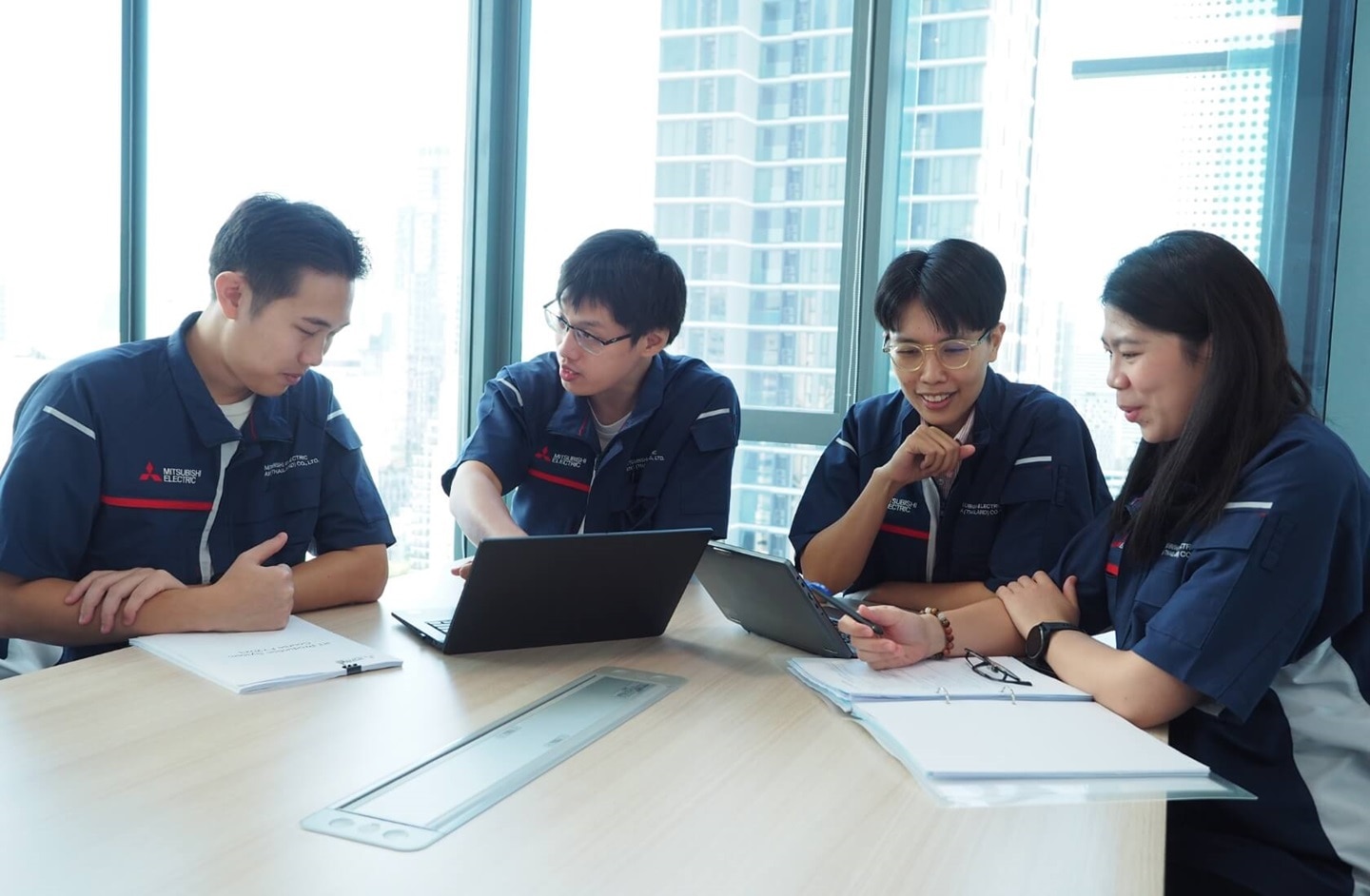
- คุณคิดว่าอะไรคือพันธกิจและหน้าที่ของแผนกวิศวกรรมการผลิตของบริษัท ME-TH คะ?
ฝ้าย:
ก่อนอื่นเลยต้องบอกก่อนนะคะว่าทาง ME-TH ของเรานั้นไม่มีโรงงานของตัวเอง แผนกวิศวกรรมการผลิตเราจะมีหน้าที่เข้าไปช่วยโรงงานต่างๆในกลุ่มบริษัท เพื่อช่วยสนับสนุนกิจกรรมการเพิ่มผลิตภาพ (Productivity) และปรับปรุงคุณภาพให้กับโรงงาน เรามุ่งหวังที่จะสร้างคุณค่าใหม่ๆโดยใส่เทคโนโลยีหรือองค์ความรู้ต่างๆที่เรามี ผนวกเข้ากับจุดแข็งของแต่ละโรงงาน ถ้าถามว่าสิ่งที่สำคัญของการผลิตคืออะไร คำตอบก็คือการที่ทุกคนสามารถทำการผลิตผลิตภัณฑ์ที่มีคุณภาพสูงเหมือนกันได้ ไม่ว่าจะเป็นใคร และในเวลาไหน โดยการที่จะสัมฤทธิ์ผลได้นั้น จำเป็นจะต้องเข้าใจถึงรายละเอียดและปัจจัยที่เกี่ยวข้องของแต่ละสถานการณ์ที่เราสามารถควบคุมได้ ยกตัวอย่างเช่น เข้าใจถึงการควบคุมกระบวนการและสามารถสร้างจิ๊ก (Jig) ที่เหมาะสมได้นั้น เรามีความจำเป็นที่จะต้องให้สมาชิกทุกคนในทีมมีส่วนร่วม ไม่ใช่การทำงานของเราเพียงคนเดียว
- คุณคิดว่าอะไรคือสิ่งที่ท้าทายในการทำงานร่วมกันกับแต่ละโรงงาน เพราะว่าในแต่ละโรงงานนั้นก็มีลักษณะเฉพาะตัวที่ไม่เหมือนกัน?
ป๊อบ:
ผมคิดว่าสิ่งที่ยากที่สุดในการเข้าไปช่วยสนับสนุนในแต่ละโรงงานคือ การที่จะทำอย่างไรให้ทุกคนที่เกี่ยวข้องนั้นมีความเข้าใจที่ตรงกันครับ ซึ่งวิธีการของเราก็คือ อันดับแรกจะเข้าไปที่หน้างานการผลิตก่อนครับ เราจะขอดูแบบ drawing ของพาร์ทชิ้นส่วนและประชุมร่วมกันกับตัวแทนของแต่ละแผนกเพื่อสร้างข้อตกลงร่วมกัน ด้วยการเปิดใจรับฟังความคิดเห็นและไอเดียที่แตกต่าง และนี่ล่ะครับที่จะทำให้เกิดความเข้าใจและความตระหนักในทุกสิ่งที่เรากังวลร่วมกัน
- คุณคิดว่าบรรยากาศการทำงานที่ ME-TH เป็นอย่างไรบ้างคะ?
ฝ้าย:
ที่ออฟฟิศ ME-TH เรามีบรรยากาศการทำงานที่อบอุ่นนะคะ พวกเรามีความสนิทสนมกันและถ้าต้องการความช่วยเหลือใดๆ เราก็สามารถพูดคุยกันได้ทุกเมื่อเลยค่ะ ไม่ว่าจะเป็นเรื่องงานหรือเรื่องส่วนตัวก็ตาม เรามีการพูดคุยกันตั้งแต่ในระดับการประชุมแบบจริงจังไปจนถึงการพูดคุยสัพเพเหระพร้อมเสียงหัวเราะร่วมกัน ต้องบอกเลยค่ะว่าเราสามารถเปิดใจพูดคุยกันได้อย่างเต็มที่ค่ะ
น้ำ:
ME-TH เปรียบเสมือนครอบครัวค่ะ พวกเรารู้สึกสบายใจที่จะพูดคุยกันกับคนอื่นๆ หรือแม้แต่หลังเลิกงาน เราก็จะมีโอกาสออกไปทานอาหารเย็นด้วยกัน ซึ่งไม่ใช่แค่ในแผนกเท่านั้นนะคะ แต่หมายถึงไปทานด้วยกันทั้งบริษัทเลยค่ะ
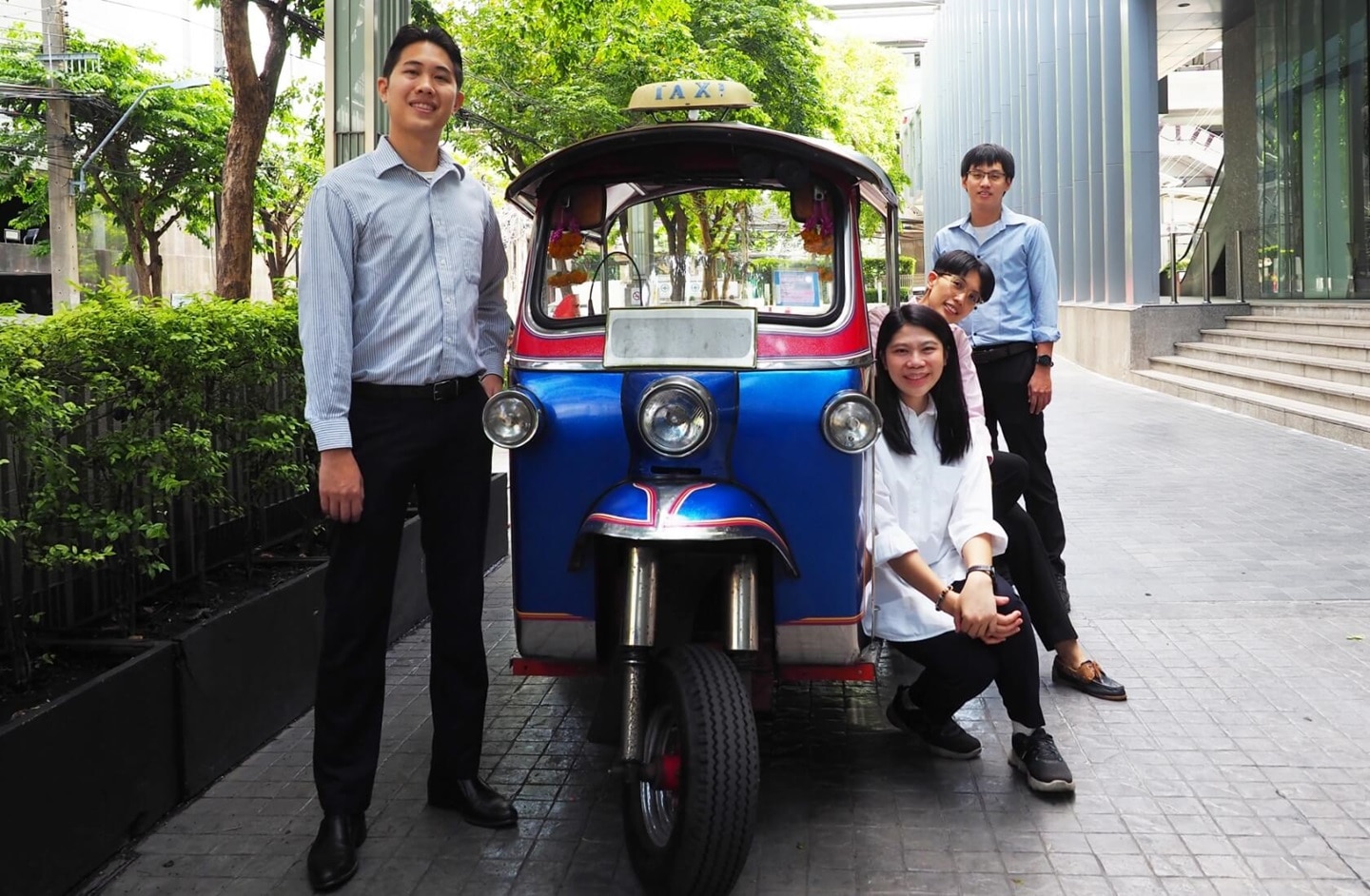
ป๊อบ:
พวกเรามีโอกาสในการพูดคุยและแลกเปลี่ยนข้อมูลกับคนญี่ปุ่นที่ทำงานที่ ME-TH อยู่บ่อยครั้ง ซึ่งในเวลางานสิ่งนี้ถือเป็นสิ่งที่สำคัญและทรงประสิทธิภาพที่จะปรึกษากันในเรื่องงาน และนอกเวลางานเราก็มีการทำกิจกรรมเพื่อสังคมร่วมกันซึ่งถือเป็นเรื่องปกติของที่นี่ครับ นอกจากนี้เรายังมีกิจกรรมหรือปฏิสัมพันธ์ร่วมกันกับวิศวกรที่ทำงานที่ประเทศญี่ปุ่นซึ่งช่วยให้เราได้เปิดโลกในมุมที่กว้างขึ้นด้วยครับ
อานันท์:
ทุกๆคนที่ออฟฟิศเป็นมิตรครับ พวกเรารู้จักซึ่งกันและกันเป็นอย่างดี ถึงแม้ว่าเราจะมาจากต่างแผนก ต่างช่วงวัยกัน แต่สิ่งนี้ล่ะครับที่ทำให้เราได้แลกเปลี่ยนมุมมองในหลากหลายมิติ และทำให้เราสามารถนำไปปรับใช้และเกิดไอเดียใหม่ๆได้ไม่ว่าจะเป็นในงานหรือเรื่องส่วนตัวครับ
หากพูดถึงความท้าทายสำหรับงานด้านการผลิต สำหรับคุณแล้วคือ?
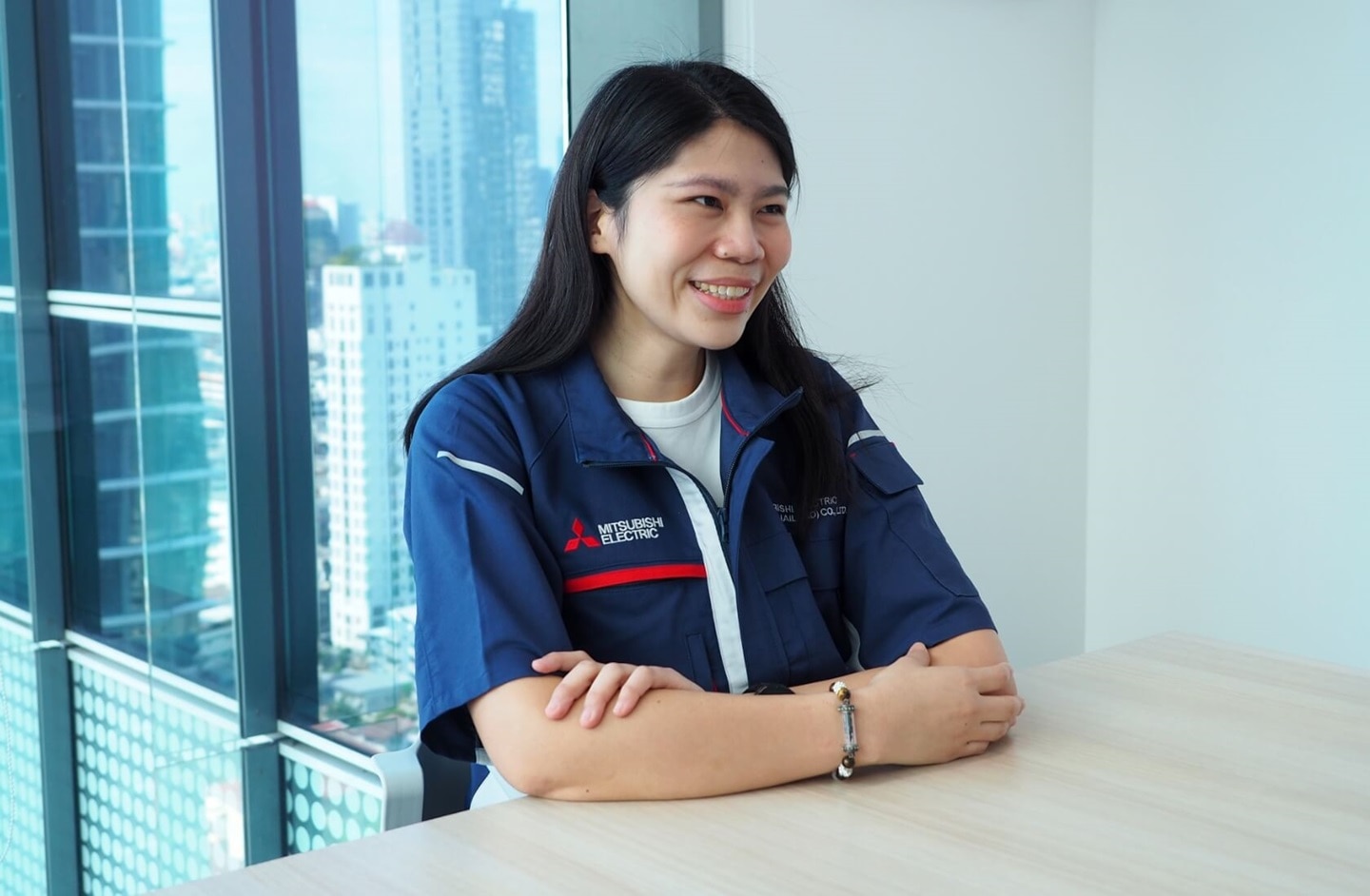
ฝ้าย: วิศวะอุตสาหการ, ผู้เชี่ยวชาญเรื่อง Just In Time (JIT), วิทยากรอบรมให้ความรู้เรื่อง JIT Kaizen ในงานสัมมนาต่างๆ
- ลำดับถัดไป เราจะมาพูดถึงความสามารถเฉพาะทางที่แต่ละคนมีความชำนาญ สำหรับคุณฝ้ายและคุณน้ำ ทั้งคู่คือผู้เชี่ยวชาญเรื่องของ Just In Time (JIT) — อยากสอบถามเกี่ยวกับงานในส่วนนี้ว่าเป็นงานที่ดูแล หรือเกี่ยวข้องในส่วนไหนคะ?
ฝ้าย:
JIT จะมุ่งเน้นในเรื่อง “การส่งมอบของที่จำเป็น ในปริมาณที่จำเป็น และในเวลาที่จำเป็น” ซึ่งต้องทำควบคู่กับการผลิตแบบ Lean และระบบการจัดการการผลิตที่มีประสิทธิภาพ ซึ่งการที่จะทำเช่นนั้นได้เราจะต้องทำการเก็บข้อมูลก่อน แผนกวิศวกรรมการผลิตของเราจะไปที่โรงงานและหน้างานการผลิต เราจะเข้าไปในฐานะคนนอกที่ไม่คุ้นเคยกับสภาพการผลิต แต่ที่จริงแล้วการเป็นคนนอกนี่ล่ะค่ะที่ถือเป็นข้อได้เปรียบ เพราะว่าเราจะสังเกตเห็นได้ถึงความผิดปกติหรือประเด็นสำคัญต่างๆที่พนักงานที่นั่นมองไม่เห็น เพราะเค้าคุ้นเคยกับสภาวะแวดล้อมเหล่านั้นและถือเป็นเรื่องปกติที่เค้าเจอในทุกวัน สิ่งแรกที่เราจะทำเมื่อไปถึงที่หน้างานการผลิตก็คือ เราจะตั้งคำถามซ้ำๆกับพนักงานที่นั่นว่าทำไมจึงเกิดของเสีย ทำไมจึงมีความผิดปกติเช่นนี้เกิดขึ้น สิ่งนี้ล่ะค่ะที่จะทำให้เราสามารถระบุถึงปัญหาที่แท้จริงหรือส่วนที่จำเป็นต้องปรับปรุงได้ค่ะ
- จริงหรือไม่ที่ Mitsubishi Electric มีรูปแบบในการทำกิจกรรม JIT แบบเฉพาะตัว?
ฝ้าย:
ใช่ค่ะ ถึงแม้ว่าแต่ละบริษัทจะรู้ว่าการทำไคเซ็น (Kaizen) แบบมีประสิทธิภาพนั้นคือวิธีการหนึ่งในการปรับปรุง แต่บริษัทส่วนใหญ่ก็จะนำไคเซ็นไปประยุกต์ใช้กับแค่กระบวนการทางตรง (Direct Process) เท่านั้น แต่สำหรับ Mitsubishi Electric เราจะมุ่งเน้นแบบบูรณาการนั่นคือ เราจะนำไคเซ็นไปประยุกต์ในส่วนของกระบวนการทางอ้อม (Indirect Process) ร่วมด้วย เราจะมุ่งเน้นไปที่ผลลัพธ์ที่ดีกว่าและทำการปรับปรุงอย่างต่อเนื่อง ด้วยแนวความคิดที่ว่า “วัฒนธรรมไคเซ็นจะต้องถูกสร้างขึ้นในทุกๆหน้างาน ในทุกๆสถานที่ทำงาน ซึ่งรวมถึงฝ่ายขาย ฝ่ายจัดซื้อ ฝ่ายผลิต ฝ่ายจัดส่ง และฝ่ายบริการ” ซึ่งนี่ถือเป็นจุดแข็งของกลุ่มบริษัทเรา กิจกรรม JIT Kaizen ควรจะทำและติดตามผลโดยพนักงานทุกคนในทุกแผนก ซึ่งรวมทั้งกระบวนการทางตรง (ฝ่ายผลิต) และกระบวนการทางอ้อม (ฝ่ายอื่นๆนอกเหนือฝ่ายผลิต)
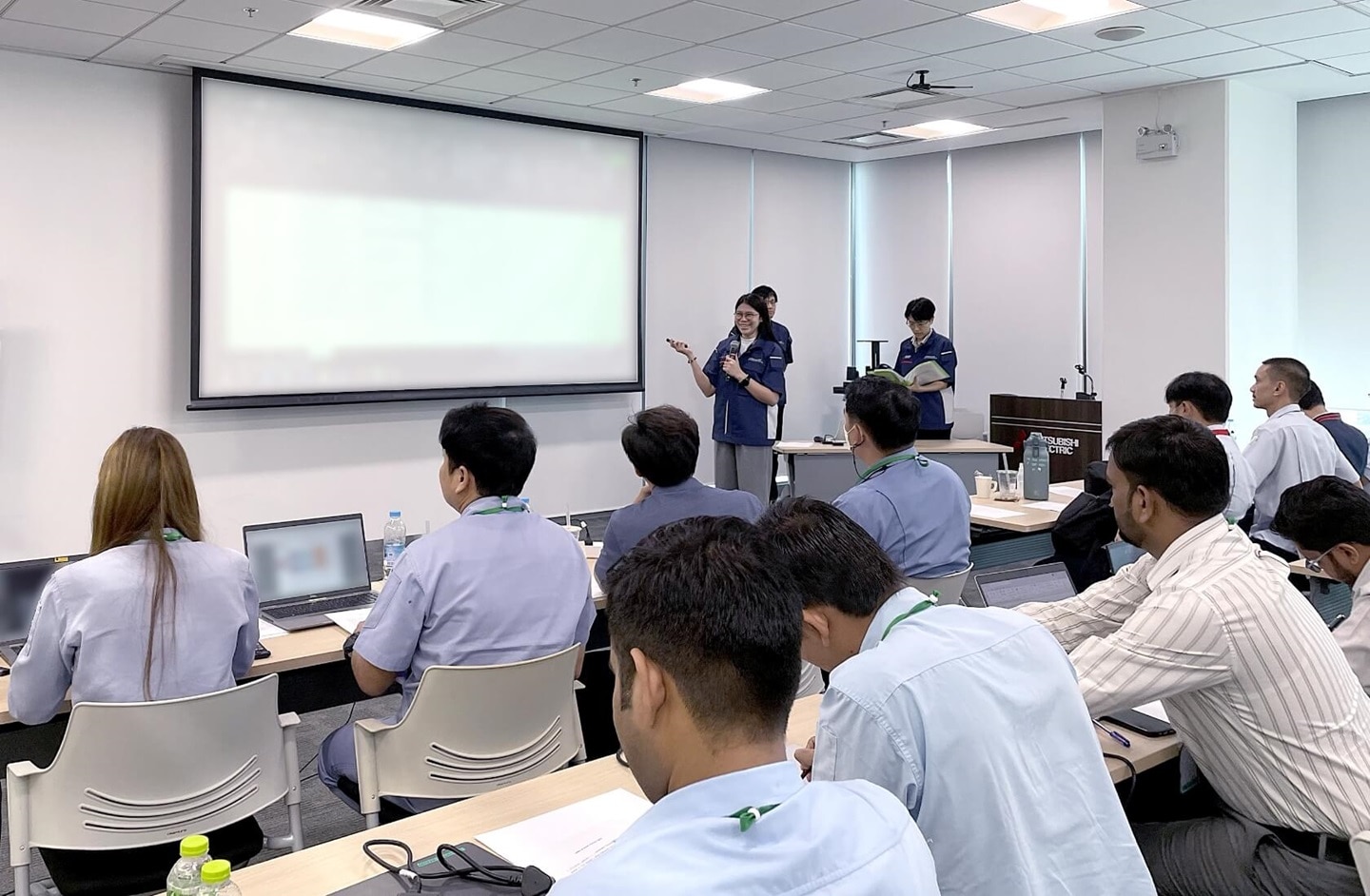
- แล้วคุณมีการนำเสนอและแชร์แนวความคิดนี้ในการทำกิจกรรม JIT อย่างไรบ้างคะ?
ฝ้าย:
เริ่มจากการนำทักษะเรื่อง JIT ที่ได้เรียนรู้จากประเทศญี่ปุ่น มาจัดสัมมนาในประเทศไทยโดยเป็นวิทยากรถ่ายทอดความรู้ให้กับพนักงานและซัพพลายเออร์ มีผู้เข้าร่วมอบรมหลากหลายแผนกจากแต่ละโรงงาน ซึ่งในความเป็นจริงแล้วก็มีความแตกต่างกันระหว่างบริบทของประเทศญี่ปุ่นและประเทศไทย และยังมีสถานการณ์ที่แตกต่างกันในแต่ละโรงงาน ดังนั้นเราจะไม่สามารถประยุกต์วิธีการที่เราได้เรียนรู้มาทั้งอย่างนั้นได้ แต่สิ่งหนึ่งที่ถือเป็นวัตถุประสงค์หลักของเราก็คือการเปลี่ยนแนวคิด (Mindset) ของพนักงาน รวมถึงการรับฟังสิ่งต่างๆจากผู้เข้าอบรมก็จะช่วยทำให้เราเข้าใจถึงบริบทของแต่ละโรงงานได้ดียิ่งขึ้นและสิ่งนี้ช่วยให้เราสามารถได้รู้ถึงความต้องการที่แท้จริงหรือจุดที่จำเป็นต้องมุ่งเน้นของแต่ละโรงงานได้
จากกิจกรรม JIT สู่การพัฒนาตนเองของแต่ละโรงงาน
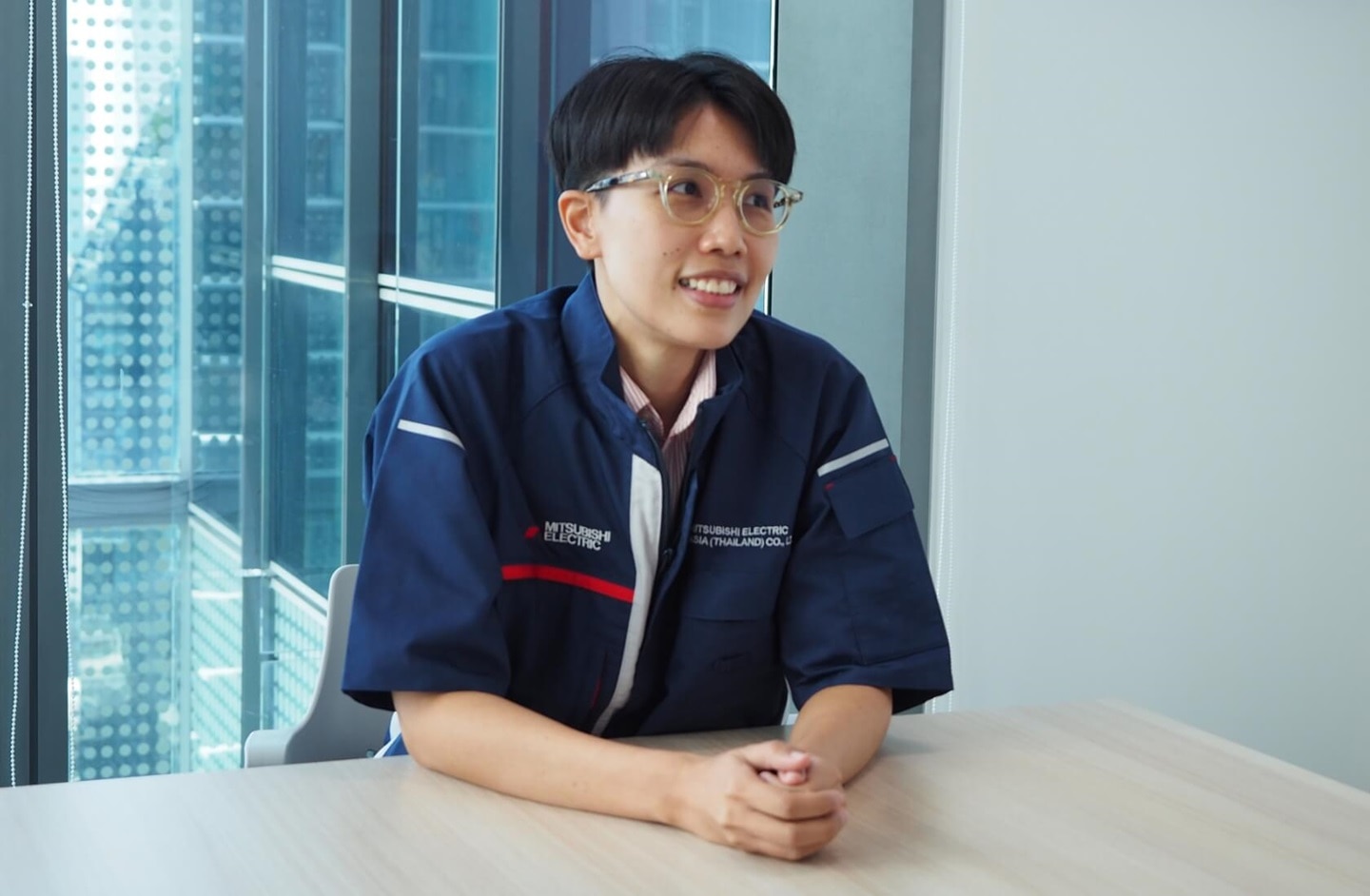
น้ำ: วิศวะอุตสาหการ, ผู้เชี่ยวชาญเรื่องการบริหารจัดการโลจิสติกส์, รับผิดชอบในเรื่องการปรับปรุงและพัฒนาโลจิสติกส์ และปรับปรุงระบบสินค้าคงคลังให้มีประสิทธิภาพสูงสุด, รวมทั้งจัดฝึกอบรมในเรื่องโลจิสติกส์และเครื่องมือ IT เพื่อเพิ่มความสามารถของทรัพยากรมนุษย์
- คุณน้ำ แล้วโปรเจกต์ JIT ที่คุณน้ำทำอยู่มีลักษณะอย่างไรบ้างคะ?
น้ำ:
ค่ะ สำหรับกิจกรรมที่ทำอยู่จะเป็นเรื่อง JIT ที่เกี่ยวข้องกับบริษัทโลจิสติกส์และโรงงานผลิตค่ะ ที่จริงแล้วโลจิสติกส์ทั่วโลกนั้นมีส่วนสำคัญกับการผลิตแบบ JIT มาก ยกตัวอย่างเช่น ถ้าแต่ละโรงงานใช้โกดังของตัวเองในการจัดเก็บสินค้า เราจะพบว่าการจัดส่งจะมีปริมาณไม่เท่ากันในแต่ละช่วง บางช่วงอาจจะพุ่งสูงมากเช่นในช่วง peak season หรือบางช่วงอาจจะต่ำมากเช่นในช่วง low season เราก็เลยมีความคิดว่าถ้าเราสร้างโกดังส่วนกลางและนำผลิตภัณฑ์ของแต่ละโรงงานมาเก็บร่วมกัน(Consolidate) และทำการจัดส่งจากโกดังส่วนกลาง วิธีการนี้น่าจะทำให้ประสิทธิภาพในการจัดการดีขึ้น ซึ่งเราตั้งเป้าไว้ว่าเราจะทำโปรเจกต์การปรับปรุงโลจิสติกส์นี้ให้เสร็จภายในปี 2025 โดยหวังว่าเราจะมีการบริหารจัดการโกดังที่ทำได้ง่ายขึ้น ลดจำนวนเที่ยวขนส่งจากรถบรรทุก และลดต้นทุนซึ่งรวมถึงต้นทุนด้านค่าเช่าโกดังลงได้ ที่สำคัญยังช่วยลดผลกระทบต่อสิ่งแวดล้อมได้ด้วยค่ะ
- การที่คุณน้ำต้องทำโปรเจกต์ร่วมกันกับทุกคนไม่ว่าจะฝั่งโรงงานรวมไปถึงบริษัทโลจิสติกส์ คุณน้ำคิดว่าอะไรคือข้อดี และอะไรคือความยากในการทำกิจกรรมคะ?
น้ำ:
สำหรับข้อดีที่ได้ก็คือการที่แต่ละบริษัทสามารถแชร์องค์ความรู้ของตัวเองให้คนอื่นได้ ถ้ามีเรื่องอะไรผิดพลาดเกิดขึ้น แต่ละบริษัทที่เกี่ยวข้องก็สามารถเข้ามาช่วยกันระดมสมองเพื่อหาทางออกร่วมกัน ในขณะเดียวกันความยากในการทำกิจกรรมก็คือการบรรลุฉันทามติร่วมกัน ยกตัวอย่างเช่นโปรเจกต์ที่น้ำทำอยู่ในขณะนี้จะมีบริษัทที่เกี่ยวข้องอยู่ทั้งหมดสี่บริษัท ซึ่งพอมีประเด็นอะไรเกิดขึ้นมาแล้วทุกคนจะต้องตัดสินใจร่วมกัน เราก็จะพบว่าในบางครั้งมุมมองที่แตกต่างกันหรือลำดับความสำคัญที่ต่างกันของแต่ละบริษัทก็อาจจะเป็นอุปสรรค์ทำให้การตัดสินใจหาข้อสรุปร่วมกันนั้นทำได้ยากมากยิ่งขึ้น
- แล้วถ้าเป็นเช่นนั้น คุณน้ำคิดว่าอะไรคือหัวใจหลักในการแก้ไขปัญหาในจุดนี้คะ?
น้ำ:
เป็นคำถามที่ดีมากค่ะ คำตอบก็คือการแชร์เป้าหมายสุดท้ายให้ทุกคนเห็นค่ะ ยกตัวอย่างเช่น หนึ่งในเป้าหมายสุดท้ายของโปรเจกต์ ร่วมกันของทั้ง 4 บริษัทก็คือการปรับปรุงประสิทธิภาพของโลจิสติกส์ และสิ่งที่เราทำอย่างต่อเนื่องก็คือการดึงองค์ความรู้และภูมิปัญญาของผู้เชี่ยวชาญแต่ละคนออกมา เรานั่งพูดคุยกันว่าเราจะดำเนินการร่วมกันอย่างไรได้บ้างที่จะทำให้ทั้ง 4 บริษัทสามารถบรรลุเป้าหมายสุดท้ายร่วมกัน ซึ่งแน่นอนว่าโปรเจกต์ใหม่และกิจกรรมใหม่นั้นเป็นเรื่องที่ท้าทายเสมอ เราจะพบว่าความคืบหน้าของงานในช่วงแรกมักจะช้า แต่ในท้ายที่สุดแล้วทุกคนจะสามารถบรรลุเป้าหมายร่วมกันได้ และนี่คือประสบการณ์อันน่าตื่นเต้นค่ะ ต้องบอกเลยว่าการบรรลุเป้าหมายร่วมกันนั้นไม่ใช่เรื่องง่าย เนื่องจากมีปัจจัยหลายอย่างที่ต้องพิจารณาร่วมด้วย รวมไปถึงปัจจัยจากเรื่องคน หลายๆครั้งที่มีคนเห็นต่างจากไอเดียที่เรานำเสนอในช่วงแรกๆ ทำให้เราต้องพูดคุยหาทางออกในสิ่งต่างๆร่วมกันอยู่บ่อยครั้งเพื่อที่จะหาสิ่งที่ดีและเหมาะสมที่สุดในการแก้ไขปัญหา บางครั้งถึงแม้เราจะได้ข้อตกลงร่วมกันที่เราคิดว่าเหมาะสมแล้ว แต่พอลองนำไปทดลองดูก็จะพบว่ามันไม่เหมาะสม พวกเราจึงต้องใส่ความพยายามเข้าไปให้ได้มากที่สุดเพื่อที่จะบรรลุเป้าหมายที่เราตั้งไว้ให้ได้ค่ะ
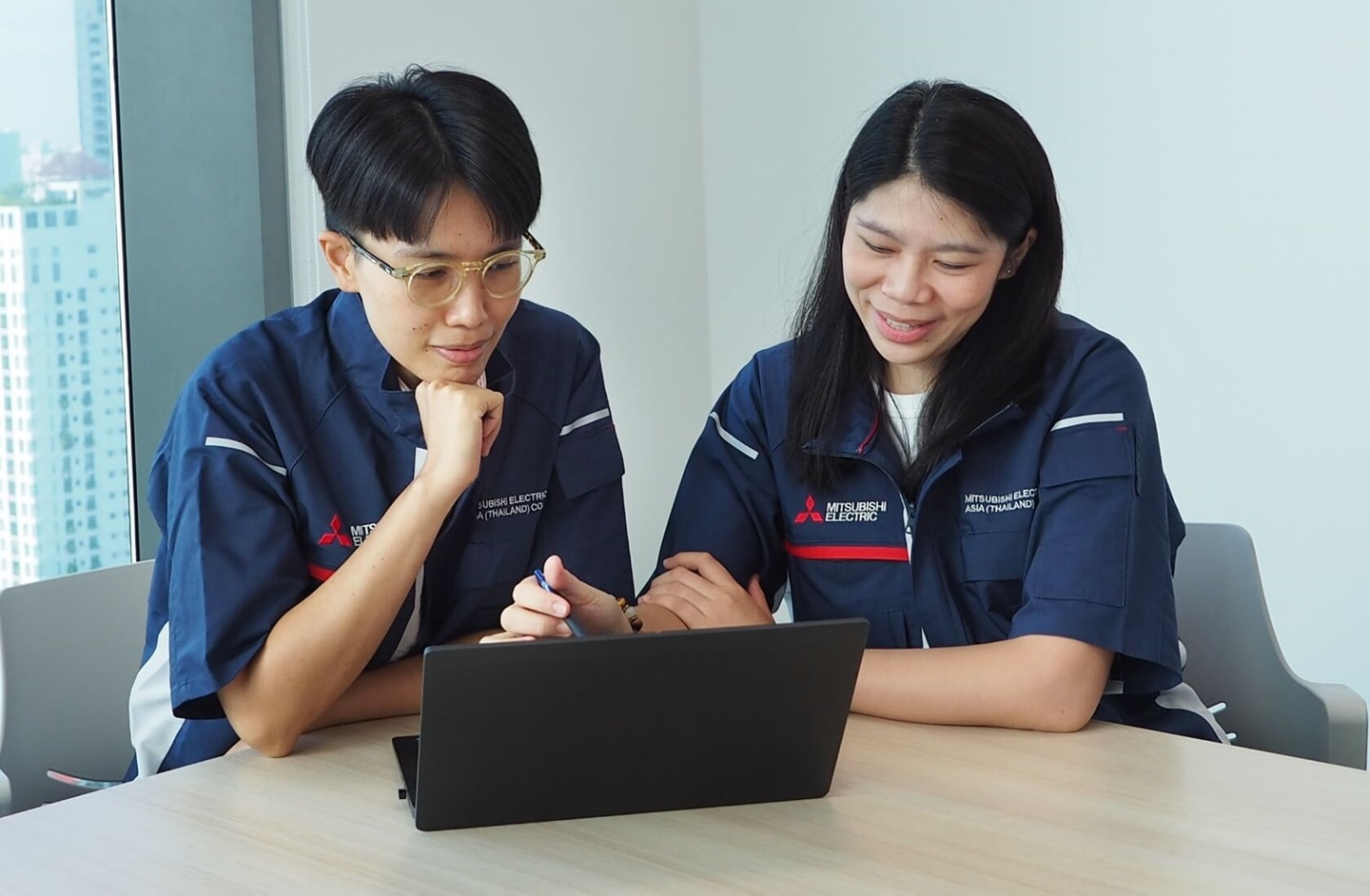
- ทำไมทางแผนกวิศวกรรมการผลิตถึงให้ความสำคัญกับคำว่า “การฝึกฝนตัวเองในฐานะโรงงานผู้ผลิต” คะ?
ฝ้าย:
ก่อนอื่นต้องเท้าความก่อนว่า ในโรงงานการผลิตแต่ละที่จะมีความท้าทายที่แตกต่างกัน ซึ่งแน่นอนว่าทีมงานของพวกเราสามารถเข้าไปช่วยสนับสนุนได้ แต่ว่าถ้าพนักงานของแต่ละโรงงานนั้นสามารถพึ่งพาตัวเองได้ รับรู้ถึงปัญหาหน้างานได้เอง และสามารถเก็บรวมรวมข้อมูลมาวิเคราะห์ได้เอง พวกเขาก็จะสามารถแก้ไขปัญหาที่อยู่ในด้านอื่นๆได้ด้วย และนี่คือสิ่งที่สำคัญในการที่โรงงานจะสามารถบ่มเพาะบุคลากรขึ้นมาเองได้ ยิ่งไปกว่านั้นในตอนที่เข้าไปที่โรงงานเป็นครั้งแรก พวกเราก็จะได้รับการสนับสนุนเช่นกัน เช่น ได้รับคำอธิบายต่างๆจากพนักงาน ได้แลกเปลี่ยนความคิดเห็นที่จะใช้ในการแก้ไขปัญหาต่างๆซึ่งการดำเนินงานด้วยวิธีเช่นนี้ มีข้อดีคือทำให้เราสามารถถ่ายทอดและเรียนรู้จากกันและกันได้ค่ะ
- คุณรู้สึกไหมคะว่า คุณกำลังมีส่วนช่วยในการยกระดับการผลิตของไทยผ่านงานที่กำลังทำอยู่?
ฝ้าย:
ใช่ค่ะ พวกเราจะอยู่ในฐานะผู้ให้ความรู้ในงานสัมมนา แต่ในขณะเดียวกันเราเองก็อยู่ในฐานะนักเรียนเวลาที่เราอยู่ที่หน้างาน และด้วยการดำเนินกิจกรรมต่อเนื่องเป็นวงจรเช่นนี้ ความรู้ที่ได้ก็จะถูกส่งผ่านต่อๆกันไปยังโรงงานอื่นๆ พวกเราเชื่อว่าสิ่งเหล่านี้จะทำให้ผลิตภาพของแต่ละโรงงานดียิ่งขึ้น และท้ายที่สุดก็จะส่งผลไปถึงการยกระดับการผลิตของประเทศไทยที่สูงขึ้น
สององค์ประกอบสำคัญ: ทำข้อมูลให้มองเห็น และแชร์ข้อมูล
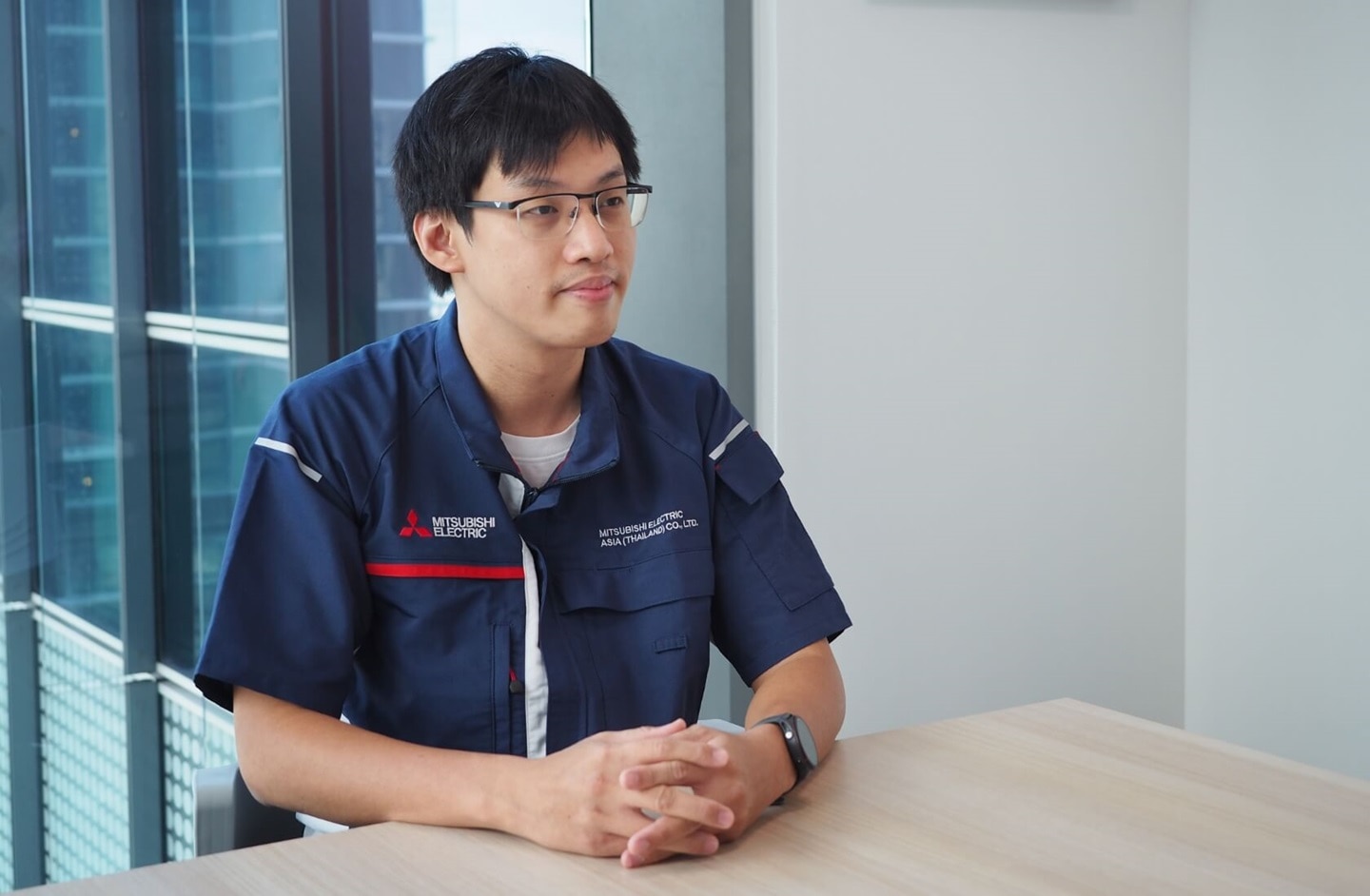
ป๊อบ: วิศวะเครื่องกล, ผู้เชี่ยวชาญเรื่องกระบวนการขึ้นรูปแม่พิมพ์พลาสติก, ปรับปรุงงานในเรื่องการควบคุมกระบวนการหล่อเย็นสำหรับการขึ้นรูปพลาสติก
- ลำดับถัดไปเราอยากจะสอบถามถึงความพยายามของคุณป๊อบและคุณอานันท์โดยเริ่มจากคำถามพื้นฐานก่อน ทำไม ME-TH ถึงมุ่งเน้นไปที่แนวความคิด “การสนับสนุนในเชิงวิทยาศาสตร์ไม่ใช่แค่จากประสบการณ์รายบุคคลเพียงอย่างเดียว”คะ?
ป๊อบ:
ครับ ในการที่จะปรับปรุงผลิตภาพของแต่ละหน้างาน สิ่งนี้ถือเป็นวัตถุประสงค์หลักของแผนกวิศวกรรมการผลิต เราต้องทำความเข้าใจกระบวนการและเครื่องมืออย่างถูกต้องแม่นยำเสียก่อน และในการที่จะทำเช่นนั้นได้ เราจำเป็นต้องรวบรวมข้อมูลทั้งในเชิงปริมาณและเชิงคุณภาพเพื่อที่จะตัดสินได้ว่ามีปัญหาอะไรเกิดขึ้นในกระบวนการผลิตและถ้าหากเจอปัญหาเราจะทำการแก้ไข ซึ่งแน่นอนว่าเราไม่ได้มองข้ามในเรื่องประสบการณ์ของพนักงาน ประสบการณ์ของพนักงานที่ชำนาญการนั้นก็ถือเป็นเรื่องที่สำคัญ แต่ภาพที่ควรจะเป็นก็คือ การที่ไม่ว่าใครก็ตามสามารถผลิตสินค้าที่มีคุณภาพสูงเหมือนกันได้ และด้วยเหตุผลนี้ล่ะครับจึงทำให้สิ่งที่เรียกว่า “ข้อมูล=ข้อเท็จจริง” ถือเป็นสิ่งที่ขาดไม่ได้ในหน้างานการผลิตครับ
- คุณป๊อบพอจะช่วยอธิบายยกตัวอย่างให้ฟังหน่อยได้ไหมคะ?
ป๊อบ:
ได้ครับ ถ้าอย่างนั้นผมจะเล่าถึงโปรเจกต์ที่ผมกำลังทำอยู่นะครับ เป็นงานที่จะต้องปรับปรุงการควบคุมการหล่อเย็นในกระบวนการขึ้นรูปพลาสติก ซึ่งในการฉีดขึ้นรูปพลาสติกนั้นจะมีกระบวนการหนึ่งที่เรียกว่าการหล่อเย็นและเราก็ตั้งใจที่จะปรับปรุงคุณภาพในส่วนนี้และลดการใช้พลังงานด้วย โดยการปรับค่าเพื่อควบคุมความเร็วในการหล่อเย็นให้เหมาะสม ในขั้นตอนแรกของโปรเจกต์การปรับปรุงเราจะต้องตรวจสอบข้อมูลจากกระบวนการก่อน เพราะว่ากระบวนการนี้ไม่ใช่สิ่งที่สามารถมองเห็นได้อย่างชัดเจน ดังนั้นเราจึงต้องอนุมานในบางจุดโดยดูจากข้อมูลที่เกี่ยวข้องเพื่อที่จะทำให้เข้าใจในภาพรวมได้ทั้งหมดครับ ซึ่งจากผลลัพธ์ที่ได้เราพบว่าการควบคุมการหล่อเย็นในกระบวนการนั้นใช้เวลามากกว่าค่าเวลามาตรฐาน นั่นหมายความว่าเรากำลังขึ้นรูปพลาสติกโดยใช้เครื่องจักรและใช้พลังงานมากเกินความจำเป็นครับ
- แล้วคุณป๊อบมีขั้นตอนในการปรับปรุงเรื่องนี้อย่างไรคะ?
ป๊อบ:
ขั้นแรกเราปรับปรุงในเรื่องการควบคุมอัตราการหล่อเย็นของเครื่องจักรครับ โดยการปรับเส้นทางของน้ำหล่อเย็นเพื่อทำให้การไหลของน้ำหล่อเย็นราบรื่นขึ้น จากนั้นในขั้นตอนที่สองเราจะทำจะการวัดค่าอุณหภูมิอย่างแม่นยำ โดยการปรับปรุงตำแหน่งของเซ็นเซอร์วัดอุณหภูมิ กล่าวคือเรากำลังทำให้การควบคุมกระบวนการหล่อเย็นมีประสิทธิภาพและเหมาะสมที่เกิดขึ้นได้จริงและโปรเจกต์นี้มีส่วนช่วยในเรื่องของความยั่งยืนด้วยครับด้วยการลดการใช้พลังงานและปรับปรุงผลิตภาพด้วยการลดต้นทุนพลังงาน และประเด็นที่สำคัญที่สุดคือการลดการปล่อย CO2 ของโรงงานการผลิต ซึ่งถ้าหากเราทำสำเร็จมันจะส่งผลกระทบเชิงบวกอันยิ่งใหญ่ทั้งภายในและภายนอกองค์กรครับ
การสื่อสารที่ดีกว่าจะนำพามาซึ่งการผลิตที่ดียิ่งขึ้น
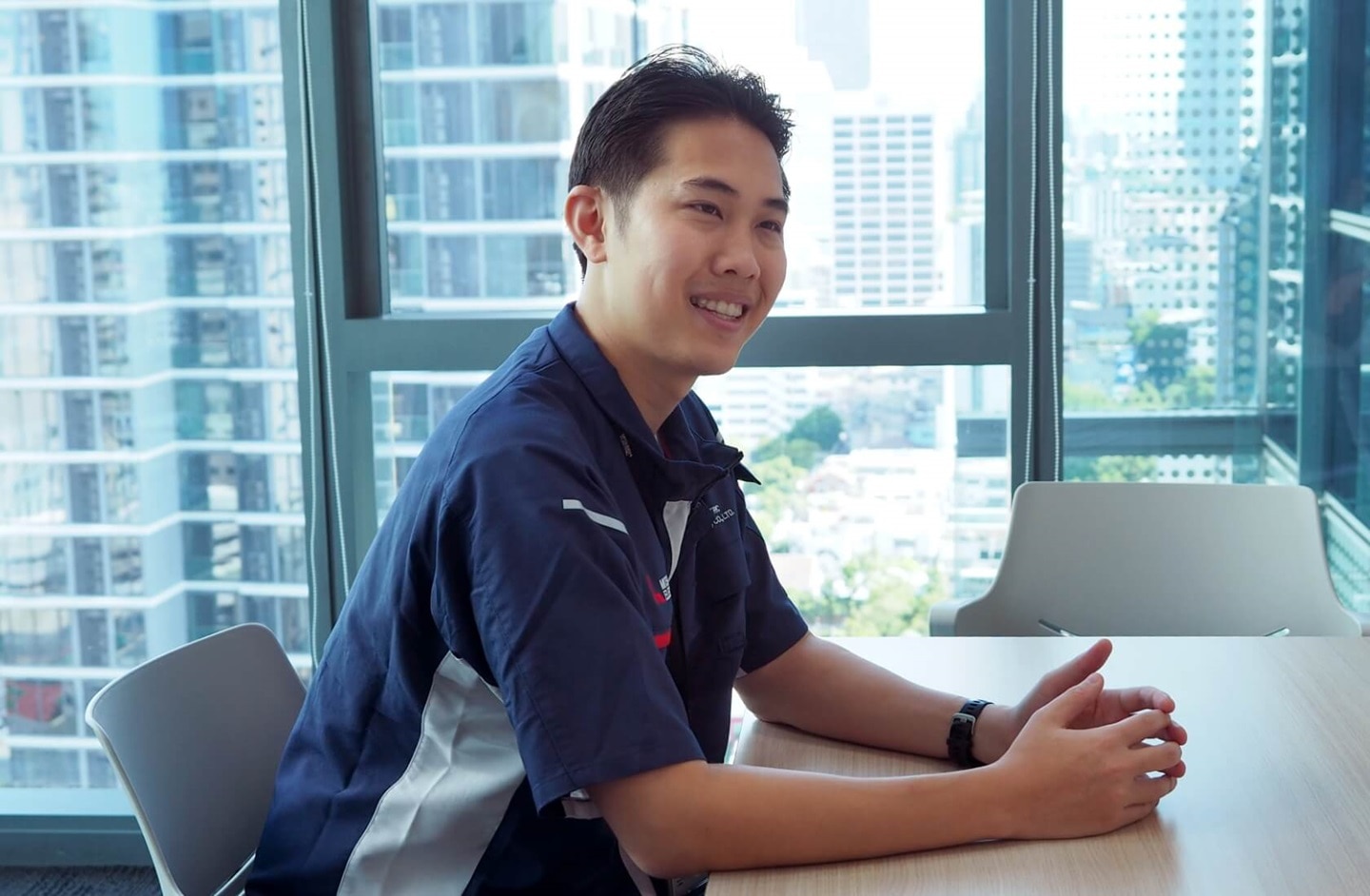
อานันท์: วิศวะเครื่องกล, ผู้เชี่ยวชาญกระบวนการ PCBA*, ปรับปรุงกระบวนการบัดกรีของ PCBA*, จัดตั้งกิจกรรมกลุ่มเฉพาะกิจของผู้เชี่ยวชาญโดยมุ่งเน้นไปที่การปรับปรุงกระบวนการ PCBA
*PCBA (Printed Circuit Board Assembly: คือแผงวงจร (PCB) ที่ประกอบไปด้วยชิ้นส่วน (Component) ต่างๆที่จำเป็น, ถือเป็นแผงวงจรที่พร้อมนำไปใช้งานในอุปกรณ์อิเล็กทรอนิกส์ต่างๆ
- คุณอานันท์พอจะเล่าเกี่ยวกับโปรเจกต์ที่กำลังทำการปรับปรุงกระบวนการบัดกรีของ PCBA ให้ฟังหน่อยได้ไหมคะ?
อานันท์:
ในแต่ละโรงงานที่เราไปนั้น เราพบว่ามีปัญหาสัดส่วนของเสียในกระบวนการบัดกรีของ PCBA ในปริมาณที่สูงมาก ผมได้ทำงานร่วมกันกับวิศวกรที่โรงงานเพื่อปรับปรุงกระบวนการ รวมไปถึงการประเมินผลลัพธ์ที่ได้และหามาตรการเพื่อกำจัดสาเหตุทางตรงของการเกิดงานเสีย และยังมีการปรึกษาร่วมกันในเรื่องการปรับสภาพของเครื่องจักรและการทำมาตรฐานคู่มือการปฏิบัติงานครับ
- แล้วเจอความยากลำบากหรือประเด็นไหนที่ให้ความสำคัญเป็นพิเศษไหมคะ?
อานันท์:
ความยากที่เจอก็คือ เราไม่สามารถหยุดการผลิตเพื่อการทดลองได้ครับ ซึ่งในความเป็นจริงแล้วเราจะต้องทำการทดลองในหลายๆรูปแบบ แต่เราสามารถทดลองได้เพียงช่วงเวลาสั้นๆในตอนพักกลางวันเท่านั้น และอีกเรื่องหนึ่งก็คือวิธีการประเมินผลการเกิดงานเสียนั้นควรจะวัดจากผลลัพธ์ของการผลิตจริงที่ได้ครับ และนั่นเลยทำให้เรายิ่งต้องระมัดระวังมากๆในการปรับเปลี่ยนการตั้งค่าเครื่องจักร ถ้าเราพบว่าเกิดงานเสียเพิ่มมากขึ้นเราจำเป็นที่จะต้องรีบปรับการตั้งค่าเครื่องจักรกลับคืนเดิม และรีบหาแนวทางอื่นๆแทนครับ
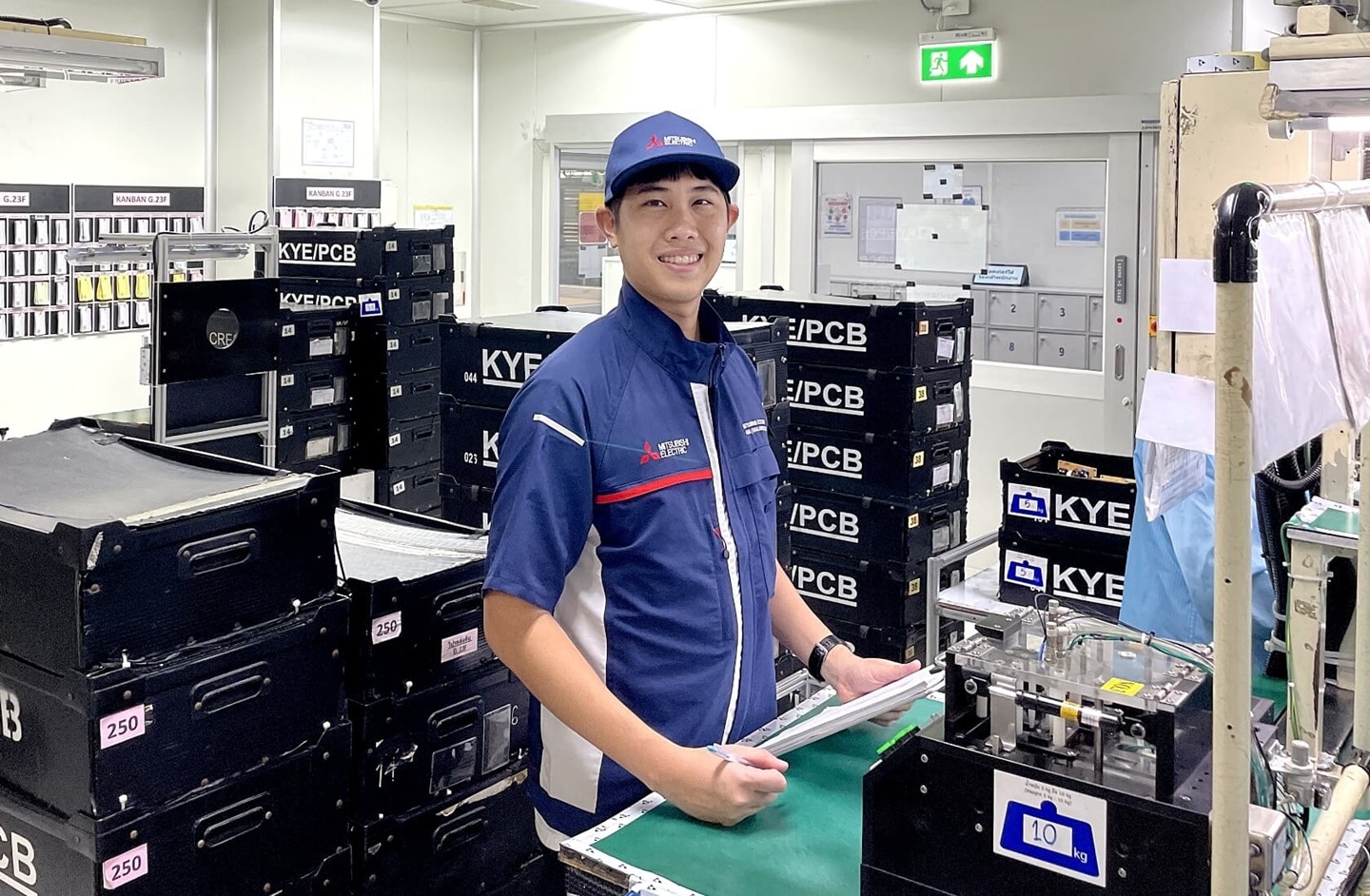
- แล้วอะไรคือคุณค่าของการทำงานในโปรเจกต์นี้คะ?
อานันท์:
ผมคิดว่าความสัมพันธ์ระหว่างผู้คนครับ ซึ่งสิ่งนี้ถือเป็นสิ่งสำคัญของการปรับปรุงผลิตภาพ ความสัมพันธ์ที่ดีจะช่วยทำให้ผู้คนพูดคุยแลกเปลี่ยนกันในเชิงลึกครับ ยกตัวอย่างเช่น ตอนที่ผมทำกิจกรรมการสัมมนาพบปะผู้เชี่ยวชาญ PCBA ผู้เข้าร่วมสัมมนาก็จะทานอาหารเย็นร่วมกันต่อเพื่อสร้างความสัมพันธ์ระหว่างกัน โดยก้าวข้ามเส้นแบ่งว่าใครเป็นอะไร หรือใครอยู่บริษัทใด และกิจกรรมสร้างความสัมพันธ์นี้ล่ะครับที่ทำให้ผู้เข้าร่วมรู้สึกสบายใจที่จะตั้งคำถามหรือสามารถให้คำตอบในเรื่องกิจกรรมการปรับปรุงกระบวนการ PCBA
- ท้ายสุดนี้ เราอยากถามเกี่ยวกับภาพในอนาคตหรือแผนการของแผนกวิศวกรรมการผลิตของ ME-TH ค่ะ?
อานันท์:
ผมขอพูดในฐานะตัวแทนของทีมนะครับ พวกเราต้องการที่จะใช้ความสามารถในการสนับสนุนกลุ่มบริษัททั้งในประเทศไทยและในต่างประเทศ โดยเฉพาะในประเทศไทยเอง อาจจะยังมีพนักงานของบริษัทในกลุ่มบางท่านที่ยังไม่รู้ว่า พวกเรามีความยินดีและพร้อมและสามารถสนับสนุนทุกคนในการแก้ไขปัญหาที่เจอได้ครับ
*ข้อมูลนี้เป็นข้อมูลล่าสุด ณ เดือนเมษายน 2024
เขียนและแก้ไขโดย Our Stories ทีม